勀傑科技 整理
引言
材料分析在晶圓製造中起著關鍵作用,幫助確定材料品質、監控製程、分析和解決缺陷問題,以及實現品質控制。這些分析結果對於確保製造過程的可靠性、一致性和最終產品的品質至關重要,因為製程設備的污染或副產物,都有可能成為晶圓缺陷的兇手,進而降低製程的「良率」。
什麼是材料分析?
所謂材料分析的意思,就是研究材料的結構、成分、性質的科學和技術領域,主要目的是獲取材料的詳細資訊,其中包含以下分析方法:
1. 表面分析: 表面分析是研究材料表面的結構、成分和性質的分析方法。它關注材料表面的特徵,包括表面形貌、表面組成、表面化學反應和表面特性等。這種分析方法可以提供有關材料表面性質的信息,並用於理解表面的特徵和行為。
常見表面分析儀器包含:掃描式電子顯微鏡 (SEM)、歐傑電子能譜儀 (AES)、二次離子質譜分析儀 (SIMS)、原子力顯微鏡 (AFM)等。
2. 結構分析: 結構分析是研究材料的晶體結構、晶格參數和原子排列方式的分析方法。它旨在了解材料的結晶特性和晶體結構對材料性能的影響。
常見結構分析儀器包含:穿透式電子顯微鏡 (TEM)、聚焦離子束(FIB)等。
3. 成分分析: 成分分析是研究材料成分和化學組成的分析方法。它用於確定材料中的元素組成和化學成分。成分分析方法可以提供有關材料中不同元素的含量和比例的信息,從而幫助理解材料的組成和性質。常用的成分分析方法包括光譜學(如紅外光譜、拉曼光譜)、質譜儀和化學分析方法。
常見成分分析儀器包含:掃描式電子顯微鏡 (SEM) 搭配X射線能量散布分析儀 (EPS)、穿透式電子顯微鏡 (TEM)、歐傑電子能譜儀 (AES)、X 光光電子能譜儀 (XPS/ESCA)等。
半導體製程如何影響晶圓良率
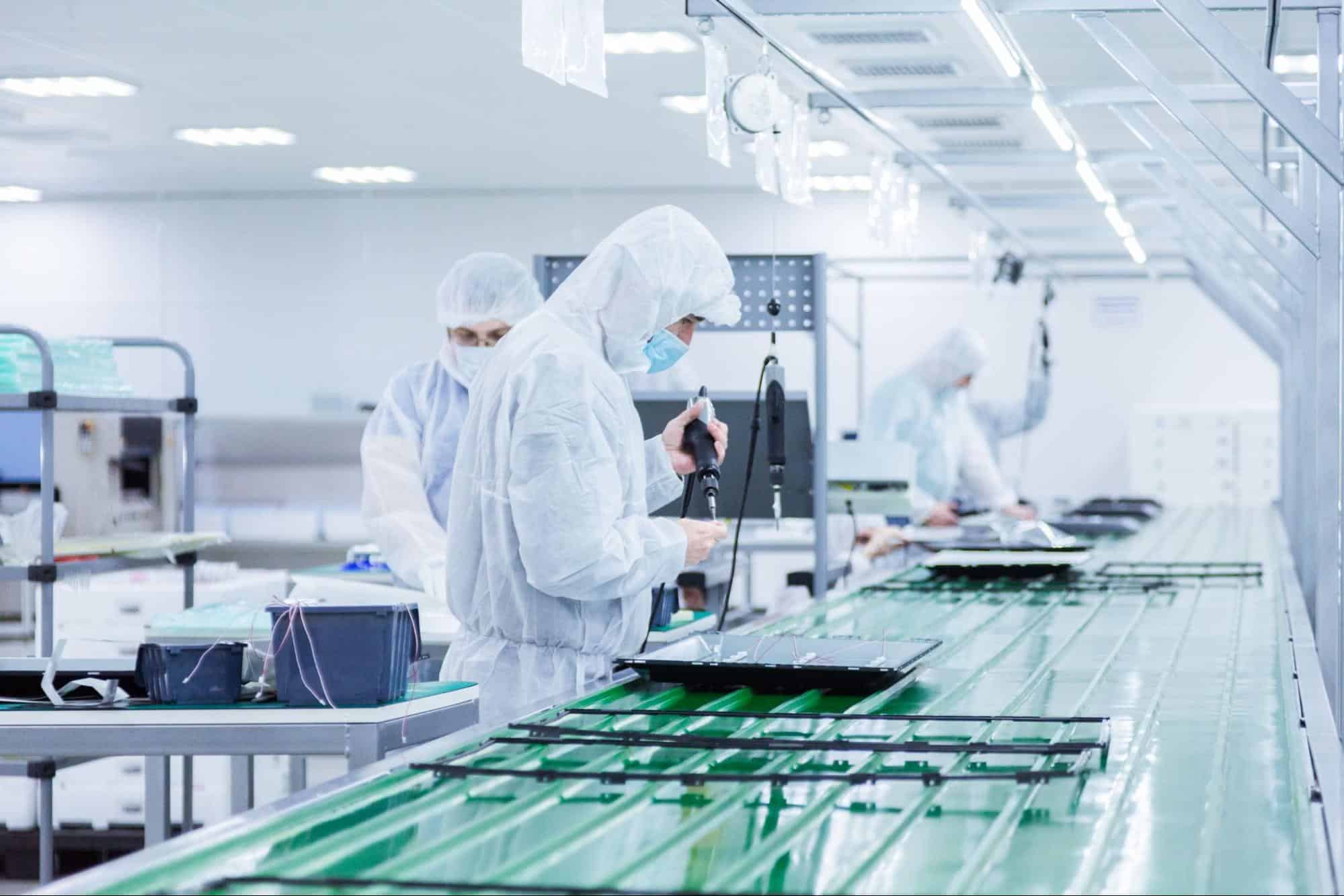
半導體製程包含從矽晶柱切成矽晶圓,經過多道製作步驟加工,再到將晶圓轉化為成千上萬個微小的半導體器件(晶片)的過程。其中可以簡單分為幾個步驟:
1. 單晶矽製造:單晶矽的製造是通過製作晶錠,這是製造晶圓的基板。在這個過程中,使用多晶矽,並加入硼酸(B)和磷(P)放入石英坩堝中高溫熔化。接著把一個種晶棒浸入熔融的矽液中,同時慢慢地旋轉並拉起來。這樣做的結果是我們得到了一個具有相同原子排列的單晶錠。
2. 晶圓製作:接著將新製成的單晶錠切割成薄片,這些薄片被稱為晶圓。由於切割後的晶圓表面可能存在凹凸不平,因此我們需要通過一系列的拋光工藝來去除這些不平整。
首先是研磨(粗拋光)、蝕刻(化學拋光)和拋光(鏡面拋光)。這些步驟可以確保晶圓的表面變得非常平滑。同時要確保拋光後的晶圓的厚度符合SEMI(半導體設備和材料國際協會)等行業標準,以確保其質量和一致性。
3. 晶圓洗淨:此步驟是為了去除沾附在表面上的異物。 異物會導致後續的晶體生長和光刻工藝出現缺陷。 一開始用雙氧水、鹽酸、氫氟酸等清洗液去除晶圓上的顆粒、金屬和有機物。之後再使用超純水去除化學溶液,接著再旋轉乾燥。
4. 晶圓表面氧化:將晶圓置於爐內,然後通過控制爐內溫度升溫,通常需要升至約800℃以上的高溫,一旦達到所需的高溫,將氧氣氣體通入爐內。這個氧氣將與晶圓表面的矽材料反應,形成氧化膜。在氧化膜生成完成後,需要精確地控制溫度和氣體流量,然後冷卻晶圓,以確保最終的氧化膜質量和均勻性。氧化膜可以提供對晶片的保護和改善其性能。
5. 曝光配線:在晶圓表面塗上一層光刻膠,這是一種光敏感的聚合物材料。光刻膠的厚度和性質會根據所需的圖形和製程參數而定。接著將晶圓置於光刻機中,使用黃光、紫外光或其他特定波長的光源來曝光光刻膠。曝光時使用一個稱為掩模的模板,其上有所需的圖形。曝光後,通過顯影過程來去除未曝光的部分光刻膠,僅保留曝光區域的圖形。接著將裸露的晶圓表面進行刻蝕去除暴露的材料或沉積新的材料。最後進行清洗步驟,以去除殘留的光刻膠和其他污染物,確保晶圓表面乾淨。
6. 晶圓測試:透過晶圓測試以快速對大量的晶圓進行測試和分類,篩選出優質的晶圓,同時排除有缺陷的晶圓。
7. 晶圓貼合:將晶圓附著在矽或玻璃等支撐基板上,這樣可以方便在運輸和處理過程中處理晶圓,同時也有助於確保晶圓的穩定性。
8. 背面研磨:完成表面圖形後,通常需要對整個晶圓的背面進行研磨以達到所需的厚度,確保晶圓的厚度均勻且符合規格。
9. 晶圓切割:將生產過程中製造的晶圓,使用金剛石製成的圓形旋轉刀片(通常被稱為劃片鋸)分離成單獨的IC芯片並密封在封裝中。
10. 封裝:完成的晶片,通過引線鍵合和重新分佈層路由到封裝基板、矽支撐基板等。然後再用諸如環氧樹脂封裝晶片,這是將完成的晶片轉換為可用於最終電子產品的關鍵步驟。
11. 部件完成:完成的半導體封裝是許多不同領域的產品的核心組件之一,它們被整合到各種應用中,例如:汽車、智能手機、IoT 設備、雲數據中心和 AI 相關產品。
而在製造過程當中,有許多因素會影響晶圓良率,其中幾個關鍵包含:
1. 製程設備污染:
製造過程中,製程設備中的零件或材料如果受到污染,會產生顆粒或者殘留物,以致晶片表面或內部出現不良缺陷。這些污染來源可能包括機械零件的磨損、材料的揮發、殘留的油脂或化學品等。
2. 製程中產生的副產物:
製程中產生的副產物是指在製程中生成的不需要的附加產物,可能是氣體、化學反應生成的副產物或者固體殘留物。這些副產物可能會附著在晶圓表面,造成腐蝕並影響晶圓的結構和性能。
在晶圓製造過程當中想要提高良率,最直接的方法就是找出污染源,以及降低副產物。但因為晶圓本身就是以奈米技術在進行製作,想要達到提高良率的效果,就必須要依賴材料分析以及適當的分析工具。
3. 製程中任何變因:
影響製程的原因很多,包含外在環境因素、人員技術操作的熟悉度或任何參數變更等等。尤其在新產品或新工藝前期,這些存在問題而造成的缺陷如果未被發現,通常使得晶圓良率偏低。
因此在晶圓製造過程當中想要提高良率,可從這些方式進行:減少污染源,降低副產物,以及量產前發現問題。但因為晶圓本身就是以奈米技術在進行製作,想要達到提高良率的效果,就必須要依賴材料分析以及適當的分析工具。
如何透過材料分析提升晶圓良率
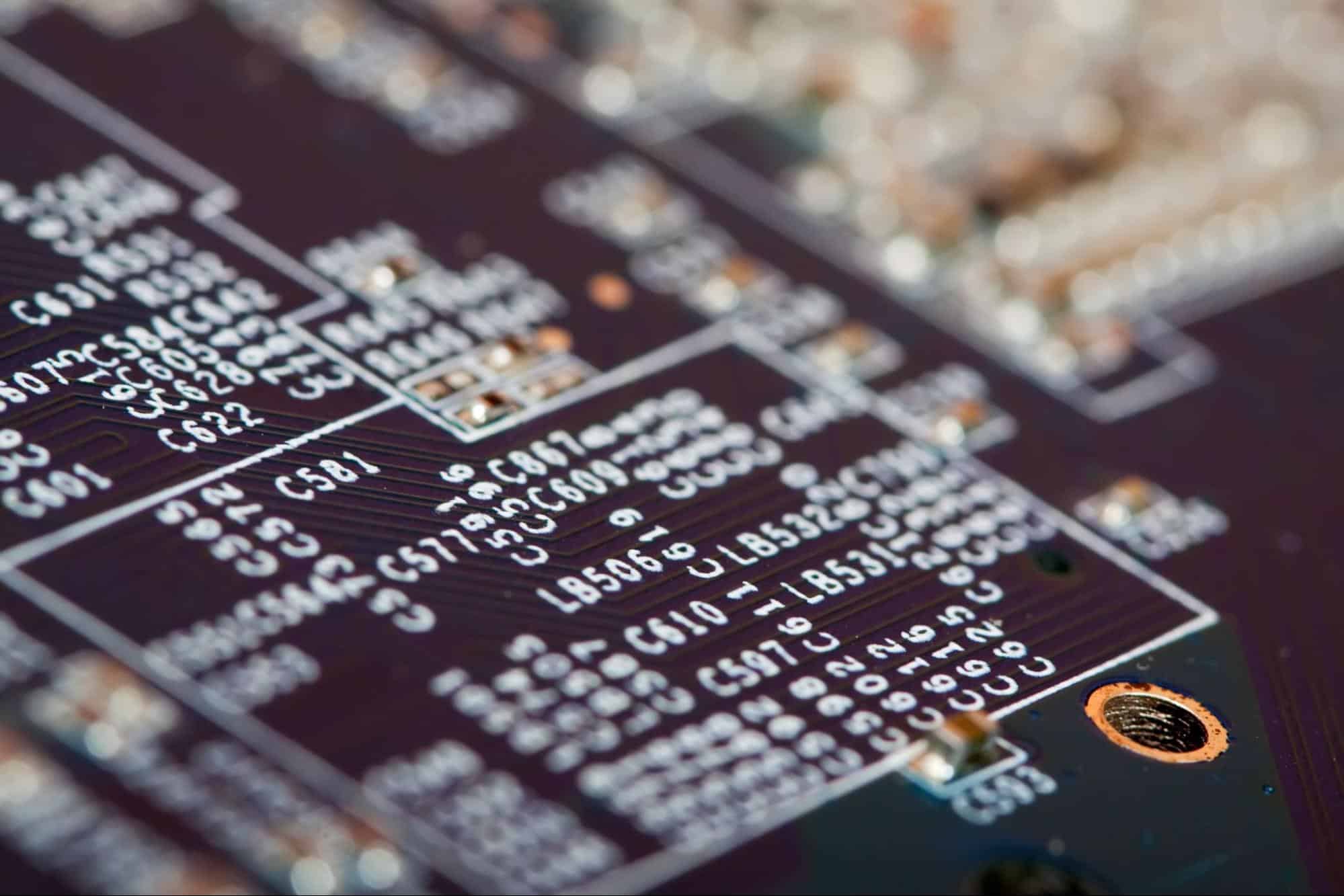
一、減少污染源:
情況一:黃光製程曝光設備,光照污染
在半導體製程中,使用黃光製程進行曝光微影時,光照污染可能是一個污染源。黃光製程中使用的光罩、光學元件和曝光機械部件可能會因微小的顆粒或塵埃而受污染,這些微粒會隨著光線進入曝光設備,留在晶圓表面或光阻層上,導致製程缺陷或器件故障。
解決方案:
1. 定期清潔和維護黃光曝光裝置的光罩、光學元件和機械部件,以減少微粒或灰塵的生成。
2. 在黃光曝光區域建立良好的環境控制,包括灰塵和顆粒物的監測和控制。使用空氣過濾系統和潔淨室技術,以減少光照污染的來源。
情況二:後製程研磨蝕刻不均勻,產生殘留物
在晶片製程的後製程中,例如研磨或蝕刻步驟,不均勻的處理可能導致殘留物的形成。當表面處理不均勻時,可能會在晶圓表面或結構之間殘留部分材料或顆粒。這些殘留物可能會影響晶片的性能,並增加晶片的失敗風險。
解決方案:
1. 工藝最佳化:最佳化後製程步驟,確保研磨和腐蝕過程的均勻性。使用精確的工藝參數和裝置,以避免不均勻的處理。
2. 清潔和檢測:在後製程步驟完成後,進行徹底的清潔和檢測,以確保從晶圓表面或結構中去除殘留物。
二、降低副產物
情況一:化學反應副產物
在半導體製程步驟中,包括沉積、蝕刻和清潔等步驟,化學反應會產生副產物。這些副產物可以是化學反應的產物或不完全反應的中間體,它們可能附著在晶圓表面、薄膜層上或器件結構中。例如,化學氣相沉積過程中產生的副產物可能是氣體分解產生的固體殘留物。
解決方案:
1. 透過SEM*搭配EDS (X射線能量散布分析儀)進行表面分析,以識別副產物的形貌、分佈及元素。這有助於確定副產物的來源並採取措施進行改進。
2. 材料替換:當知道副產物的來源時,可以透過SEM檢測不同保護層材料在蝕刻前後的表面形貌及結構,找出更適合且低副產物的保護材料。舉例:氧化矽、氧化鋁為常見的保護層材料,但氧化釔可以提供相同的保護卻可明顯減少副產物。
*透過SEM找晶圓缺陷問題,需切割為晶片取樣
情況二:機械加工副產物
在製程中的機械加工步驟,例如研磨、蝕刻和拋光,也可能產生副產物。這些副產物可以是切削或研磨過程中產生的微細顆粒、碎片或殘餘材料。它們可能留在晶圓表面或結構中,導致污染或影響晶片的性能。
解決方案:
1. 透過SEM檢測殘留物的表面形貌,初步判斷可能的副產物的來源。
*透過SEM找晶圓缺陷問題,需切割為晶片取樣
三、量產前測試與失效分析
如上所述,半導體製程有一連串步驟,包括晶圓最終將切割、封裝,而成為我們所使用的晶片。製程中有任何缺失都可能造成晶圓缺陷,導致晶片失效,這時就需要使用SEM等相關檢測儀器去做失效分析,找出問題原因,再去優化製程。
解決方案:
1. 為了提高晶圓良率、在量產前提早發現問題,可依據情況所需先做小批量晶片試產檢測或相關材料檢驗。
SEM (掃描式電子顯微鏡) + EDS (X射線能量散布分析儀):材料分析的基本配備
由上可知,在進行材料分析的時候,針對不同層面的分析,會需要用到多種的分析工具,一般廠商通常會先自行做一些初步的晶圓缺陷與污染源判別,如果還是無法改善才會選擇轉交給專業的材料分析公司。
1. 在表面分析方面:SEM可以提供高解析度的表面形貌和粗糙度圖像,檢測並顯示樣品表面的微觀結構,例如凹凸、孔洞和紋理。這有助於評估晶圓的表面品質、均勻性和形狀。
2. 在結構分析方面:SEM可收集背向散射電子(BSE)成像來看樣品,觀測比二次電子(SE)成像再更深層的區域。也能進一步切片做截面分析,觀察晶片內部結構問題。
3. 在成分(元素)分析方面:SEM搭配EDS (X射線能量散布分析儀)能檢測並識別污染源或副產物的元素,快速識別及判斷可能的來源。
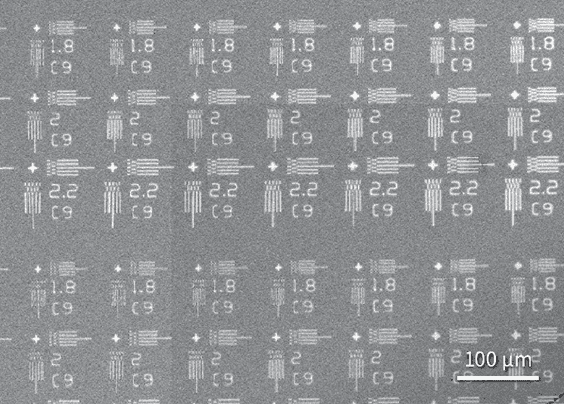
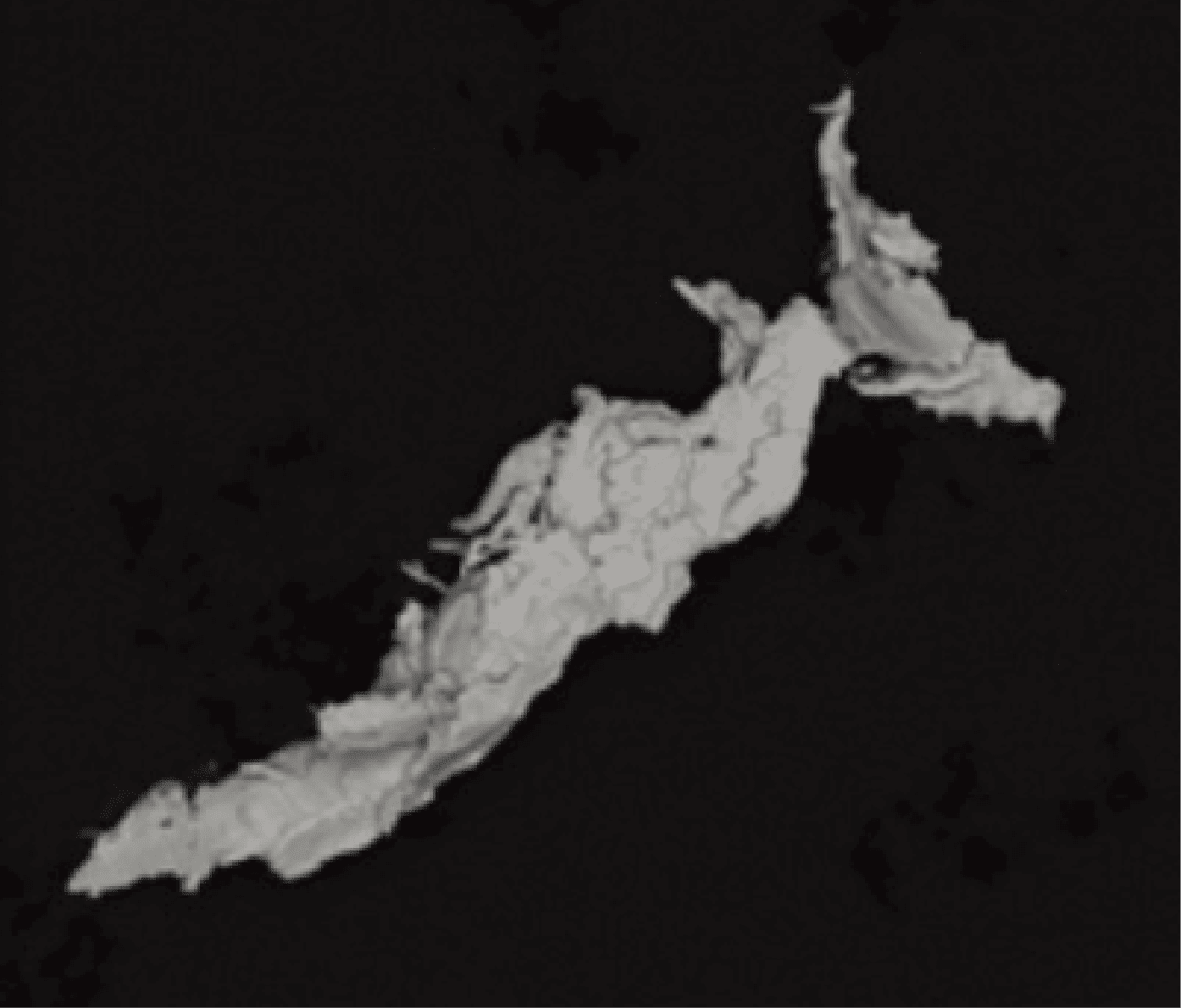
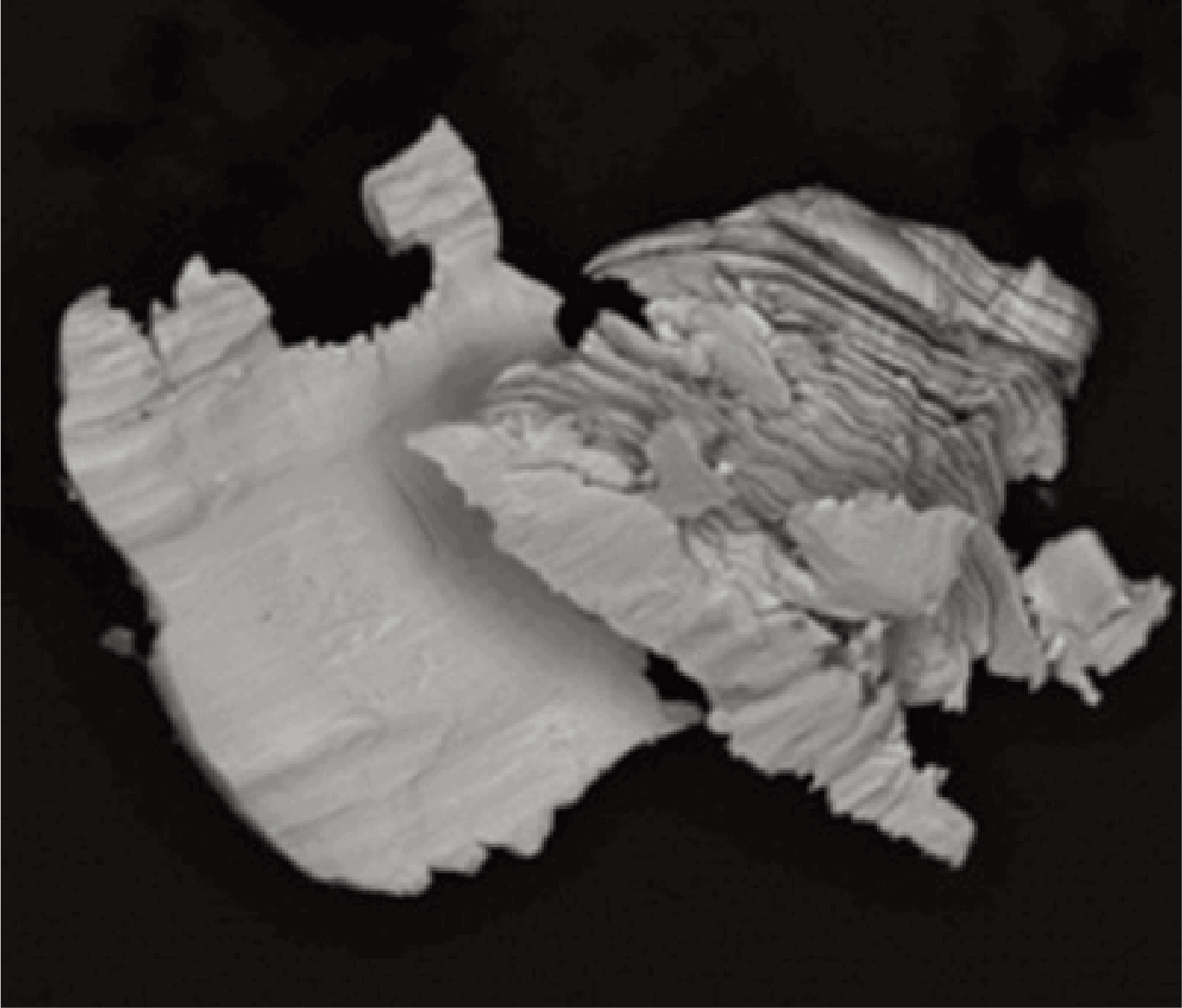
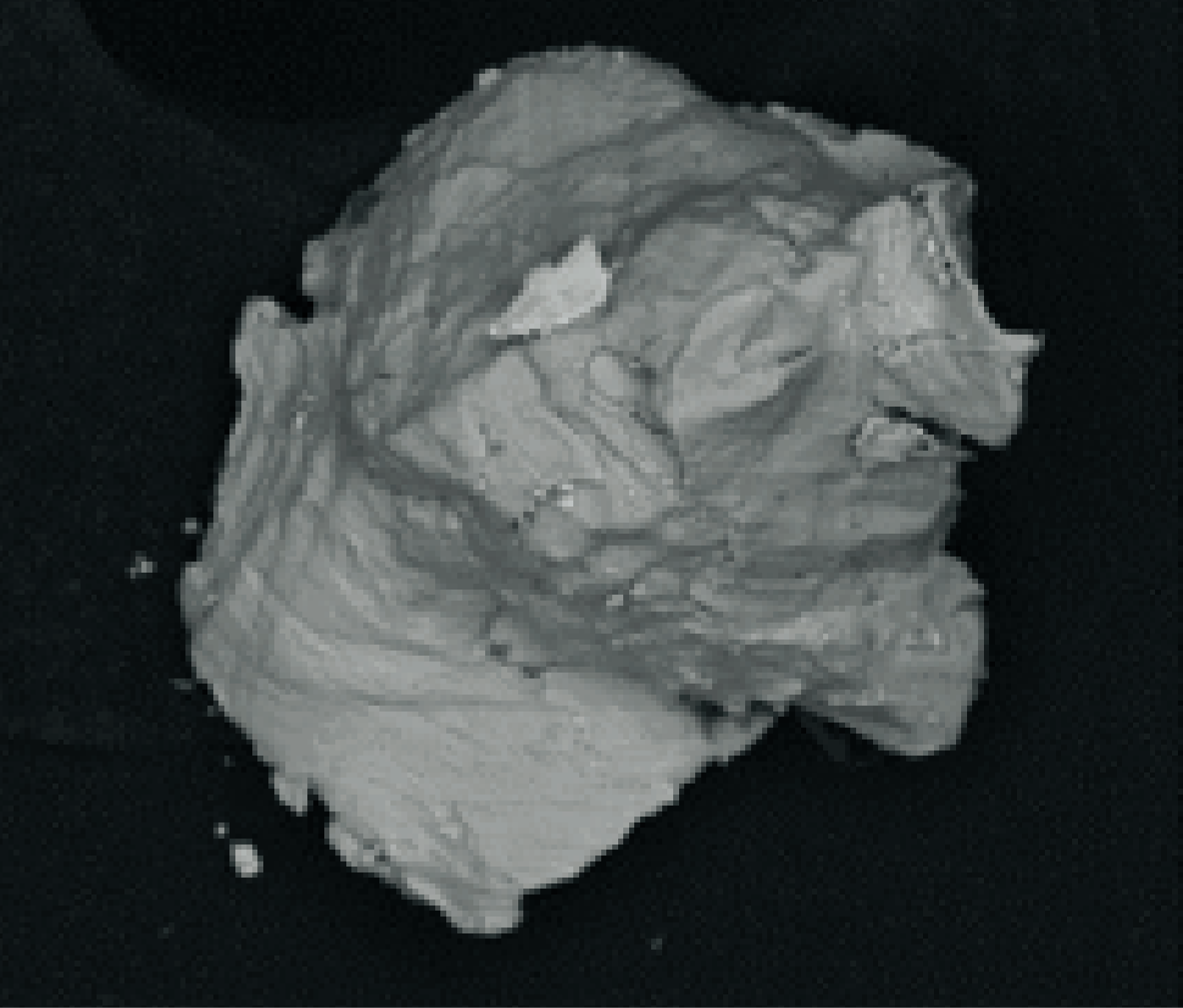
用SEM做材料分析,發現汽車零件清洗後仍有殘留污染微粒
結語
對於半導體製程來說,使用掃描式電子顯微鏡(SEM)做材料分析,其優點為可快速簡單取得結果,有利於推進製程效率。當然,SEM還是有其觀測限制,必須依據實際情況妥善運用各儀器配合以達到最佳目的。
近年來,SEM已走向小體積的桌上型趨勢,Phenom系列的桌上型SEM還可依據應用需求擴充各種功能,如:3D粗糙度重建、孔徑統計分析、粒徑分析量測等,甚至能設定參數實現自動化檢測。未來,SEM在半導體產業的應用層面將更加廣泛。
若您有掃描式電子顯微鏡(SEM)檢測等相關需求想要討論,或想要更進一步了解更多相關知識!
歡迎來電/來信 洽詢
TEL: 02-2218-0148 & 0800-888-963
Email: sales@kctech.com.tw
勀傑官方Line帳號:@kctech
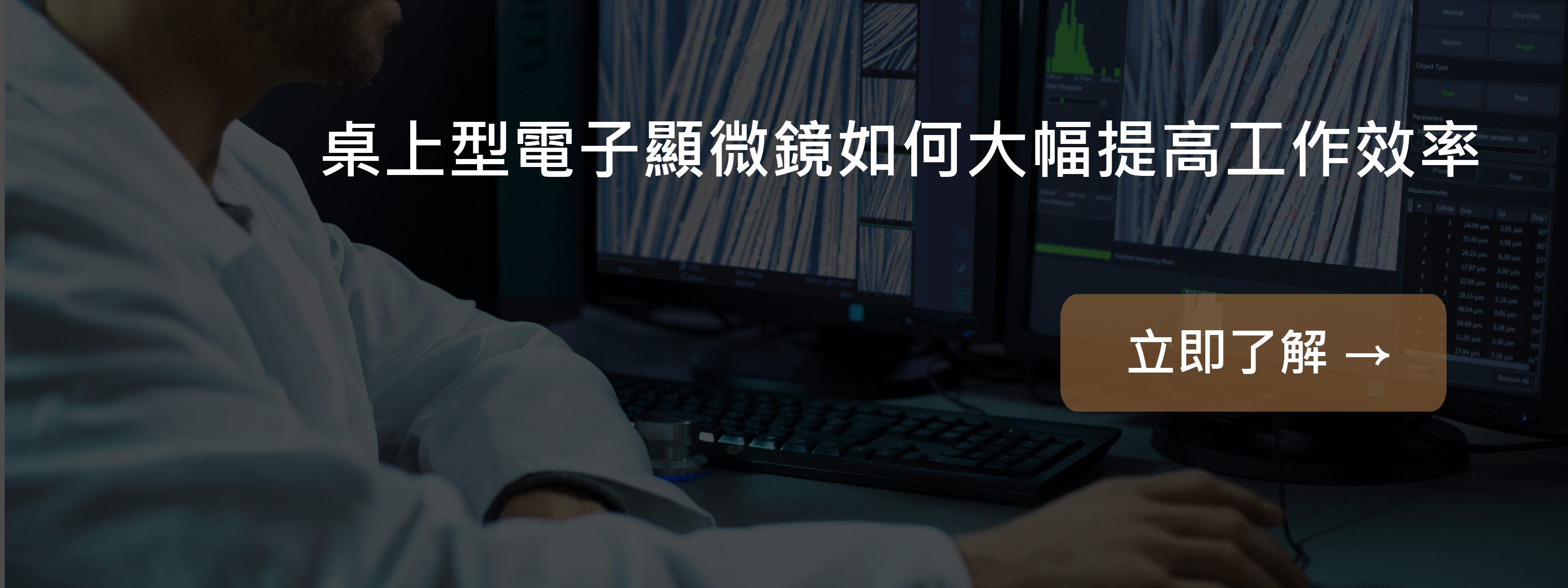
更多電鏡影像知識與延伸閱讀: